Union Millwrights Thriving in Wind Industry
Late in 2017, MidAmerican Energy announced that they planned to spend one billion ($1,000,000,000) “repowering” approximately 706 older turbines across Iowa. The “repowering” would include replacing blades, hubs and turbine parts, which would allow each turbine to produce between 19 and 28 percent more energy. For the Millwrights at North Central States Regional Council of Carpenters, this was welcome news. The repowering would bring additional work allowing the millwrights to demonstrate their expertise in this area. The 10-15 year old wind farms were certainly in need of these much-needed upgrades.
With the advancement of technology and new incentives in the form of available federal tax credits, more owners were making the choice to install lighter, longer blades that can sweep more wind with every rotation. Updated electronics and more efficient turbines make the repowering more attractive than replacing the entire 200-300-foot wind turbines. As a result, the wind industry is thriving, and the amount of renewable energy being produced is substantially greater.
During re-powering, millwrights remove the old blades and replace old components with more productive components one piece at a time. Then, using a massive crane and intricate rigging, about six men carefully guide new blades weighing over six tons each onto a new hub. When all three blades are matched up, the new blades and hub, weighing as much as 45 tons are lifted and re-attached to the tower about 280 feet above the ground.
Eric Kilpatrick, Millwright from Local 1463 in Omaha NE, the General Foreman at the Adair and Iowa site for Mortenson Energy Services is supervising a repowering crew that is becoming increasingly efficient while always maintaining safety standards in the field. Eric said, “If any one of my guys sees something unusual or unsafe, they have the power to stop the process and resolve the issue before continuing. I empower everyone with that ability.” Conversely, the non-union contractor just down the highway on the same project recently dropped a wind blade creating a potentially dangerous and deadly situation for the workers. The drop also caused a one-week safety shut down, and it was not the first time. A previous drop of a wind blade by that same contractor resulted in Mortenson’s site also being shut down despite their impressive safety record and expert equipment handling.
Mortenson started this project turning over one wind tower every three days. Now, they have created efficiencies reducing the ratio to one tower every ten hours. On the other hand, a nearby non-union contractor on another part of the project was turning over one wind tower every week. They have progressed to one tower every three days. In fact, Eric’s crew has quadrupled the output the non-union contractor. The output has been so significant the owner of the wind towers hired Mortenson’s union employees to supplement the non-union contractor who fell far enough behind to compromise its federal tax incentives. Not only has Mortenson been able to assist less efficient non-union contractors, they also maintained the re-power schedules on their own contracted towers.
What’s the secret? Mortenson is bringing in young workers and giving them an opportunity to demonstrate their skills. They are respected for their work ethic and practice the importance of being a “union” member. “Everybody counts on each other. We make sure that Mortenson can deliver strong outcomes and be recognized in the wind power industry. People need to know that when Mortenson bids on these jobs, they are getting the very best,” said Kilpatrick.
Jonathan Phelps, a millwright from Local 1176 in Fargo ND, said it perfectly, “I want to make sure the next guy is better than me.” He describes the work environment as one that instills a culture of learning that will help every union millwright on the job be more successful. “While every union member is expected to get their training hours in, we still expect our co-workers to get a lot of on-site training,” said Phelps.
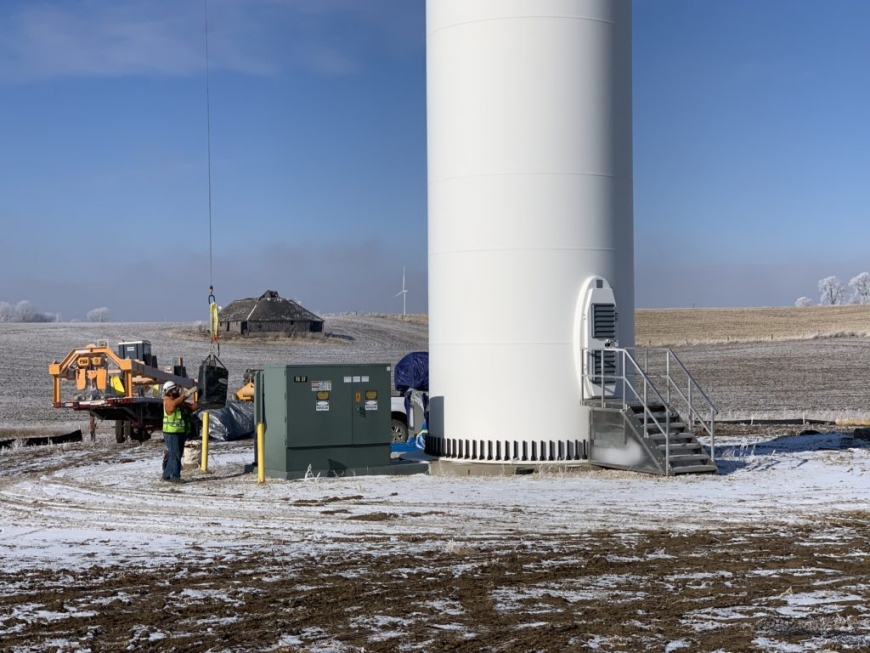
Photo: Jonathan Phelps prepares new parts and supplies to be hoisted up into the wind turbine.